
Separatory płuczek
Zapraszamy Państwa do zapoznania się z technologią oczyszczania błota i recyklingu płuczek wiertniczych. Ta nowoczesna technika wiertnicza pozwala wiercić na płuczkę wiertniczą nowocześnie, oszczędnie i wydajnie.
Do najważniejszych zastosowań urządzeń do recyklingu i oczyszczania płuczek zaliczamy wykorzystanie tych urządzeń w technologii horyzontalnych przewiertów sterowanych, przy wierceniach na płuczkę na prawy obieg wiertnicami pionowymi (budowa studni, odwierty pod pompy ciepła), przy oczyszczaniu popłuczyn powstających w procesie produkcji kostki brukowej oraz przy robotach mikrotunelowych.
Firma MARPOL Technologie Bezwykopowe posiada 25-letnie doświadczenie w projektowaniu i produkcji tych urządzeń. Nasze pierwsze separatory były wykorzystane do wierceń pod studnie głębinowe i przy przewiertach sterowanych HDD w pierwszej połowie lat 90-tych.


Zdjęcia powyżej – budowa sieci sanitarnej metodą przewiertu sterowanego HDD w gminie Czosnów koło Warszawy w 2015 roku. Na budowie wykorzystano technologię oczyszczania płuczek urządzeniem MARPOL SOP-800.
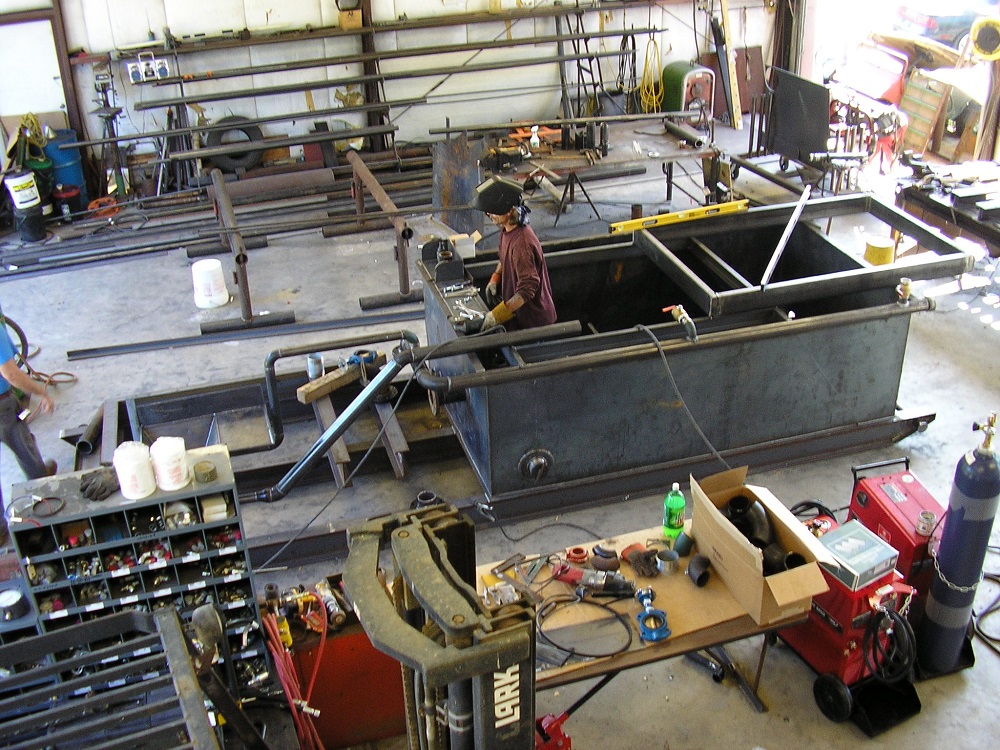
Zdjęcie powyżej – budowa systemu separacji zwiercin MARPOL SOP-600H (hala produkcyjna w firmie MARPOL – wrzesień 2004).
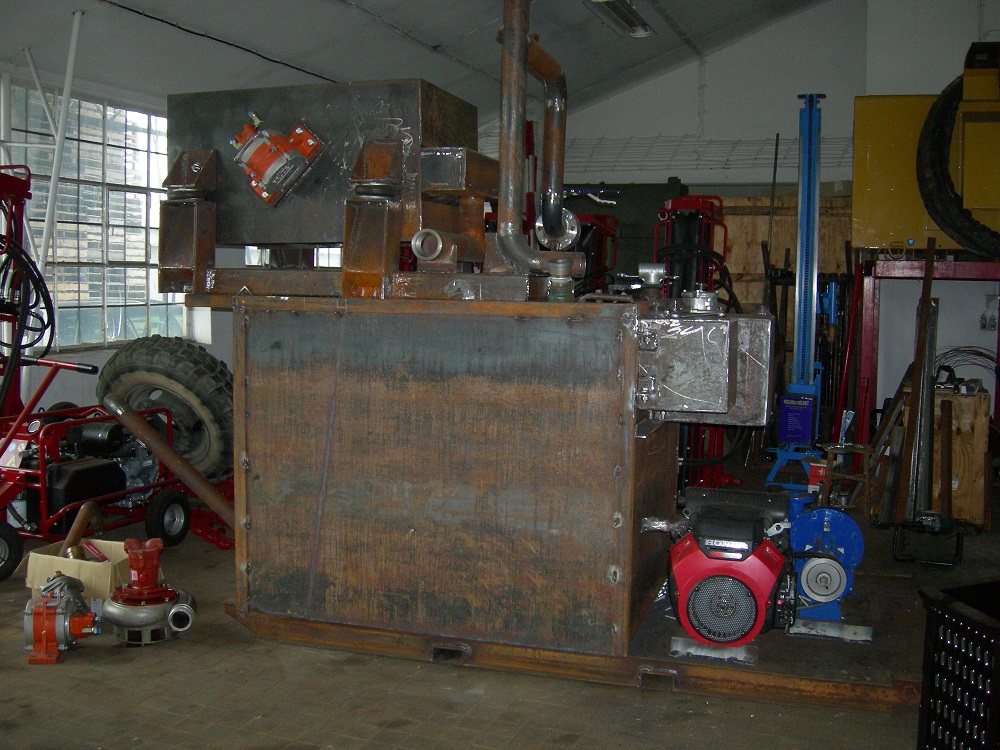
Zdjęcie powyżej – budowa systemu separacji zwiercin MARPOL SOP-400H z konterem o pojemności 2000 l dla potrzeb wiertnicy płuczkowej do wierceń pod studnie pompy ciepła do 150 m (hala produkcyjna w firmie MARPOL – lipiec 2008)
SYSTEMY SEPARACJI ZIERCIN DLA WIERTNIC STEROWANYCH HDD KLASY 150-300 kN
Budowa sieci gazowych niskiego, średniego i wysokiego ciśnienia, sieci wodociągowych oraz kanalizacji sanitarnych i burzowych metodą bezwykopową z wykorzystaniem technologii horyzontalnych przewiertów sterowanych HDD (ang. Horizontal Directional Drilling) w połączeniu z recyklingiem płuczek wiertniczych i separacją zwiercin za pomocą urządzenia wiertniczego klasy średniej do 200 kN siły ciągu.
Zintegrowany system wiertniczy to zestaw urządzeń do budowy sieci gazowych i wodno-kanalizacyjnych metodą bezwykopową z wykorzystaniem technologii horyzontalnych przewiertów sterowanych, zwany dalej SYSTEMEM. W skład SYSTEMU wchodzi urządzenie wiertnicze na gąsienicach o sile ciągu około 200 kN, żerdzie wiertnicze na odległość 150 m, zestaw narzędzi wiertniczych, kontenerowy system mieszania i separacji zwiercin oraz system lokalizacji. SYSTEM przeznaczony jest do wykonywania przewiertów sterowanych pod przeszkodami, takimi jak rzeki, jeziora, tereny uzbrojone, ulice, place, chodniki itp. Prace wiertnicze nie powodują degradacji środowiska naturalnego.
Przewierty sterowane to bezwykopowa technologia układania rur na potrzeby gazownictwa, telekomunikacji, wodociągów, kanalizacji, energetyki i drogownictwa. Zadanie wiertnicze realizowane jest w trzech etapach – pilot sterowany, rozwiercanie, instalacja rurociągu:

Tradycyjna metoda przewiertów sterowanych HDD
Tradycyjna metoda wiercenia wymaga przygotowania i podania do otworu wiertniczego bardzo dużej ilości czystej płuczki wiertniczej a błoto bentonitowe (mieszania płuczki wiertniczej i zwiercin wydobytych z otworu wiertniczego) stanowi odpad budowlany, który należy poddać utylizacji – wywiezienia z placu budowy za pomocą wozów asenizacyjnych i złożenia w miejscu składowania odpadów budowlanych. Ta metoda wiercenia jest typowa dla maszyn wiertniczych w klasie średniej dla urządzeń wiertniczych o sile ciągu do 200 kN.
Zapotrzebowanie na płuczkę wiertniczą jest proporcjonalne do wielkości zadania wiertniczego – np. podczas instalacji tą metodą rurociągu o średnicy 400 mm na odległość 150 m zapotrzebowanie na płuczkę wiertniczą (tym samym na wodę) jest na poziomie 150-200 000 litrów (30-40 beczek o pojemności np. 5 000 l). Ta ogromna ilość płuczki powiększona o około 40-50 000 l zwiercin musi być podczas realizacji tego zadania fizycznie wywieziona z placu budowy, co prowadzi do spowolnienia robót wiertniczych i dużych kosztów związanych z utylizacją odpadu budowlanego, jaki jest błoto bentonitowe.
Duża ilość płuczki, jak jest potrzebna na budowie, to również znaczne spowolnienie robót wiertniczych z powodu konieczności dostarczenia tak dużej ilości wody na budowę oraz potrzeby wymieszania wody z bentonitem. Zazwyczaj taki cykl przygotowania płuczki wiertniczej trwa około jednej godziny (w tym czasie można przygotować np. około 5 000 l płuczki, która zostanie zużyta np. po 20-30 minutach). W rezultacie wydajność wiertnicy sterowanej jest silnie ograniczona i zazwyczaj oscyluje na średnim poziomie 500-600 mth rocznie. Można powiedzieć, że większość czasu wiertnica właściwie nie pracuje a czeka na płuczkę. Ogromne zapotrzebowanie na płuczkę stanowi to „najwęższe gardło” technologii przewiertów sterowanych HDD i ma duży wpływ na rentowność tej działalności.
Zintegrowana metoda przewiertów sterowanych HDD
Metoda zintegrowana HDD polega na zastąpieniu zespołu tradycyjnych mieszalników systemem recyklingu płuczki wiertniczej i separacji zwiercin w trybie ciągłym. Zintegrowany system wiertniczy pozwala na wykorzystanie tej samej płuczki wiertniczej wielokrotnie a stała frakcja zwierconej formacji geologicznej jest efektywnie odseparowana od błota bentonitowego – do utylizacji pozostaje piach, żwir, glina itp. w ilości odpowiadającej objętości otworu wiertniczego (w metodzie tradycyjnej do wywiezienia z placu budowy jest wielokrotnie więcej).
Ponadto w tej metodzie występuje efekt znacznego zwiększenia wydajności wiercenia – wiertnice wyposażone w systemy oczyszczania płuczek osiągają zazwyczaj 2-3-krotnie większą wydajność, która dochodzi do 2000-2500 mth rocznie. Wiertnica po prostu nie czeka tak długo na wodę i płuczkę, ponieważ płuczka wiertnicza krąży w obiegu zamkniętym a do wywiezienia z placu budowy jest frakcja sucha, której jest mniej i owa frakcja nie jest odpadem budowlanym, co stanowi o przewadze tej technologii w stosunku do metody tradycyjnej również pod względem ochrony środowiska naturalnego.
Oprócz zwiększenia wydajności ma miejsce obniżenie wielu składników kosztów, w tym. między innymi – kosztów związanych z mniejszym zużyciem wody (zużycie spada o 50-80%), mniejszym zużyciem bentonitów i polimerów, mniejszym zużyciem paliwa w samochodzie, który nie musi tak często kursować tam i z powrotem po wodę i z obniżeniem kosztów wywozu błota bentonitowego i utylizacji odpadów budowlanych.
Urządzenie do recyklingu płuczki i separacji zwiercin, zwanym w skrócie SOP (System Oczyszczania Płuczki) ma postać kontenera o masie około 7 ton. System SOP jest stawiany na samochodzie ciężarowym na miejsce zespołu mieszalników beczkowych i pełni podwójną funkcję – występuje w roli mieszalnika płuczki wiertniczej i w roli urządzenia do oczyszczania błota bentonitowego, czyli do oddzielenia zwiercin (urobku wydobytego z otworu wiertniczego za pomocą płuczki wiertniczej) od płuczki wiertniczej. W efekcie końcowym oczyszczona płuczka wiertnicza jest kierowana ponownie do urządzenia wiertniczego.
Proces oczyszczania płuczki wiertniczej w urządzeniach do oczyszczania płuczek wiertninczych produkowanych przez firmę MARPOL
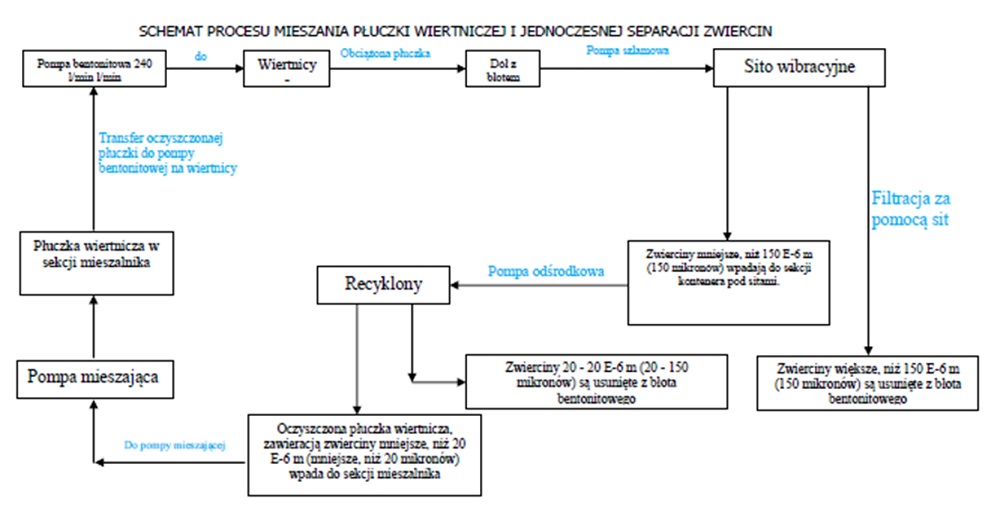
Opis szczegółowy procesu oczyszczania płuczek wiertniczych
1. Mieszanie. Mieszanie wody z bentonitem do 1-szy etap procesu. Mieszanie następuje w sekcji mieszalnika, który jest wypełniony wodą w ¾ jego objętości.
2. Oczyszczanie płuczki. a) Z chwilą rozpoczęcia wiercenia czysta płuczka wiertnicza jest transferowana • z sekcji mieszalnika płuczki do pompy bentonitowej na wiertnicy sterowanej. • w wyniku postępu procesu wiercenia w dołach technologicznych gromadzi się błoto bentonitowe (płuczka wiertnicza obciążona zwiercinami). b) W następnym kroku następuje transfer błota bentonitowego (za pomocą dodatkowej pompy szlamowej) do sekcji sit. Zadaniem sekcji sit jest wstępne odseparowanie zwiercin większych od 150 mikronów. c) Wstępnie oczyszczona płuczka jest kierowana z sekcji sit do sekcji recyklonów, gdzie następuje odseparowanie zwiercin większych od 20 mikronów.
3. Oczyszczona płuczka wiertnicza jest transferowana do sekcji mieszalnika, skąd jest ponownie kierowana do pompy bentonitowej na wiertnicy, co zamyka cykl obiegu płuczki.
4. Dodatkowe elementy wyposażenia: pompa hydrauliczna odśrodkowa z agregatem hydraulicznym do transferu błota i generator prądotwórczy do zasilania systemu SOP (w przypadku wersji elektrycznej):

Powyżej pompa hydrauliczna odśrodkowa z agregatem hydraulicznym. Zadaniem pompy jest transfer błota do maszyny SOP.
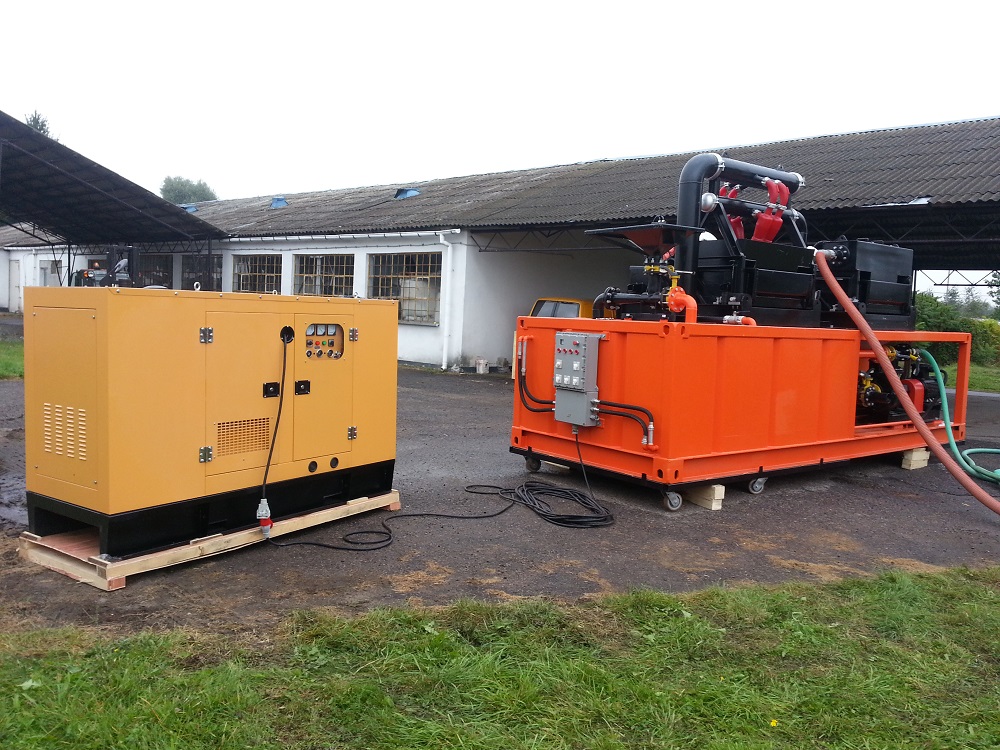
Powyżej agregat prądotwórczy o mocy do zasilania systemu SOP-800.
Wdrożenie technologii oczyszczania i recyklingu płuczek wiertniczy prowadzi do zmniejszenia zużycia wody i ma bezpośredni pozytywny wpływ na ochronę środowiska, ponieważ technologia w takiej wersji nie generuje odpadów budowlanych.
Obniżeniu ulegną również koszty związane ze stosowaniem technologii przewiertów sterowanych HDD i zwiększeniu ulegnie wydajność wiercenia w skali roku, co przyczyni się do tego, że inwestycja będzie bardziej rentowna.
Wdrożenie u klienta technologii budowy sieci gazowych, wodno-kanalizacyjnych i teletechnicznych metodą przewiertu sterowamego z zastosowaniem technologii recyklingu płuczki i separacji zwiercin, z wykorzystaniem zintegrowanego systemu wiertniczego jest realizowane przez firmę Marpol w następujący sposób:
1. Kompletacja poszczególnych komponentów technologii zgodnie ze specyfikacją zamówienia a następnie ich dostawa do użytkownika.
2. Dobór środków transportu (minimalny zestaw to samochód ciężarowy i przyczepa niskopodwoziowa) i zabudowa systemu SOP na samochodzie przez dostawcę technologii w siedzibie dostawcy (użytkownik odbiera SOP już na samochodzie).
3. Szkolenie w siedzibie użytkownika w zakresie projektowania przewiertów sterowanych, zasad bezpieczeństwa podczas wykonywania przewiertów, obsługi i konserwacji urządzeń, doboru płuczek wiertniczych i hydrauliki otworowej, organizacji placu budowy.
4. Samodzielne wykonanie pilota przez użytkownika.
5. Samodzielne wykonanie przewiertu wraz z instalacją rurociągu przez użytkownika.
6. Coroczne konsultacje i doszkolenia dla personelu użytkownika przez dostawcę.
7. Uwzględnienie posiadanej technologii wiertniczej w projektach budowlanych realizowanych przez przedsiębiorstwo użytkownika.
8. Udział użytkownika w przetargach publicznych i sektorowych, w których występują roboty budowlane realizowane w technologii bezwykopowej.
9. Sukcesywne nawiązywanie współpracy z innymi przedsiębiorstwami z branży wiertniczej i prezentacja technologii oczyszczania płuczek u swoich partnerów biznesowych.
ZASTOSOWANIA SYSTEMÓW OCZYSZCZANIA PŁUCZEK I ZAWIESIN PRODUKOWANYCH PRZEZ FIRMĘ MARPOL
1. Horyzontalne przewierty sterowane HDD
2. Odwierty pionowe metodą płuczkową na prawy obieg (studnie i odwierty geotermalne pod pompy ciepła).
3. Oczyszczanie popłuczyn w procesie produkcji kostki brukowej.
4. Mikrotuneling
